The DVSA's updated Guide to Maintaining Roadworthiness was released in April 2018. At the time of it's release there were a reported 73,458 goods vehicle operator's licenses and 8,836 bus and coach operator's licences in circulation. What that should mean is that over 80,000 copies of the newly updated guide ought to have been downloaded by HGV or PSV operators and that by now, at the end of summer 2018, those updates and new guidance should be incorporated into operators' safety and maintenance procedures. Especially, as previous editions of the Guide made clear, and the latest edition emphasises; it is the operator's responsibility to ensure that its vehicles and trailers are safe on the road.
The Importance of The Guide:
The purpose of the Guide is unchanged. It is published to offer guidance to operators on the steps that they ought to take in order to ensure that their vehicles are safe on the road.
The Guide is endorsed by the Traffic Commissioners and is frequently referred to in Public Inquires. When DVSA vehicle examiner officers visit operators to carry out maintenance assessments, they make specific reference to the Guide (and to the DVSA's Categorisation of Defects, if they find anything wrong with vehicles or trailers).
It is trite, but nevertheless relevant, to observe that knowing what the Guide says will not only help operators keep their vehicles and trailers safe, but it will also mean that they are more likely to satisfy the DVSA at any assessment (and so avoid the issue of prohibitions or the threat of being called to Public Inquiry).
So What is New?
The good news for operators is that the Guide is not a complete re-write (and it would be odd if it was, because many of the fundamentals set out in previous editions are just that). Much of the material will therefore be familiar and for operators who were already following the 2014 edition of the Guide this update ought to help not hinder.
That being said, it is worth operators noting the following:
More detailed guidance relating to IT for Vehicle Maintenance Systems
- This guidance had previously been published as a separate standalone document, but it has now been incorporated into the Guide. The guidance provides details on what a good IT maintenance system should do including some of the key features of a computerised system (for example, the capability to print hard copies of maintenance records upon request) and advice on how to keep electronic maintenance systems secure.
- Guidance is also provided on what is becoming an increasingly common method of using electronic handheld devices for the completion of walk around checks.
Maintenance facilities - adequacy and accreditation
- Whilst the general list of what a maintenance facility should include is largely the same (with reference now being made to emissions testing equipment), the new Guide adds an advisory note that for operators who do their own maintenance, it is important that they ensure that their own in-house facilities are adequate for the job.
- To this is added the strong recommendation that workshops and fitters are accredited.
Tyre Management
- Given that, according to the DVSA, tyre defects are among the most common safety related problems that they come across, it is no great surprise that there is the addition of a new section on a Tyre Management System, which includes advice on checking a tyre's age, the appropriateness for the vehicle, the importance of making sure that staff dealing with tyres are properly trained, and that drivers are equipped to recognise and report tyre issues.
Brake Performance
- This is another section which has been substantially extended with the inclusion of guidance which had previously been published elsewhere - this time, in relation to Electronic Braking Performance Monitoring Systems (EBPMS) which the DVSA acknowledges can be effective in supplementing maintenance arrangements, including recommending the use of an EBPMS for trailer brake testing.
- Perhaps more importantly, the Guide states that it is 'essential' that whichever system is used for brake testing at regular safety inspections it must be capable of providing evidence of the performance results which can be included in, or appended to, the safety inspection sheet.
- Operators should expect to be marked down if the DVSA finds that the brake test results are missing, and they should not assume that an entry "Road Test - brakes ok" will be sufficient.
Emissions
- Predictably, given the widespread press coverage on emissions and Emulator 'cheat devices', the Guide includes a new section providing guidance on the maintenance of vehicles' emissions control systems - with specific reference to operators and drivers ensuring that AdBlue levels are correctly maintained.
Updated Sample Defect Report Sheet and Safety Inspection Sheet
- In line with some of the new recommendations discussed above, the sample walk round check sheet has been amended to include a check for AdBlue (as well as a check for vehicle height), whilst the sample regular safety inspection sheet now includes a section to record road test brake temperatures.
- More is also made of the importance of operators monitoring the work that is done to check their vehicles and trailers, and as the Guide states "Continuous reviewing and monitoring of the quality of the systems in place is essential to ensure that they are sufficiently comprehensive to do the job". The daily vehicle and trailer checks (frequently carried out by drivers immediately before they drive) are highlighted as being especially important, as is the importance of effectively monitoring these checks and the way in which they are recorded.
Monitoring - Earned Recognition
- There is a new section in the Guide explaining how the DVSA's new "Earned Recognition Scheme" works and what operators are required to demonstrate to be eligible. Click here for more information on this Scheme.
Goodbye to Annex Four
- The graph which had previously been recommended for assessing the suitable safety inspection frequency interval has been disposed of and replaced with a table, setting out a range of operating conditions which it is recommended are used as the new basis for the right interval to use.
- Operators wishing to change the inspection intervals need to ensure that any changes are recorded using the Vehicle Operator Licensing ('VOL') system online. Usefully, the Guide includes a number of Case Studies setting out how inspection intervals can be set and explaining what updates to VOL are required.
What Should Operators Do?
- Download and read the new Guide (click here to view), transport managers and those working for them in the traffic office ought to know what the Guide says.
- Review the systems and records already in place and consider what changes, if any, need to be made.
- Ensure that all maintenance providers whether internal or external, have access to, and have read the new Guide.
- Make a note of the changes, and take action - few if any operators will have nothing to do to ensure that the new Guide's updated recommendations are followed.
Richard P. Pelly © June 2018. Article first appeared in Croner-I.
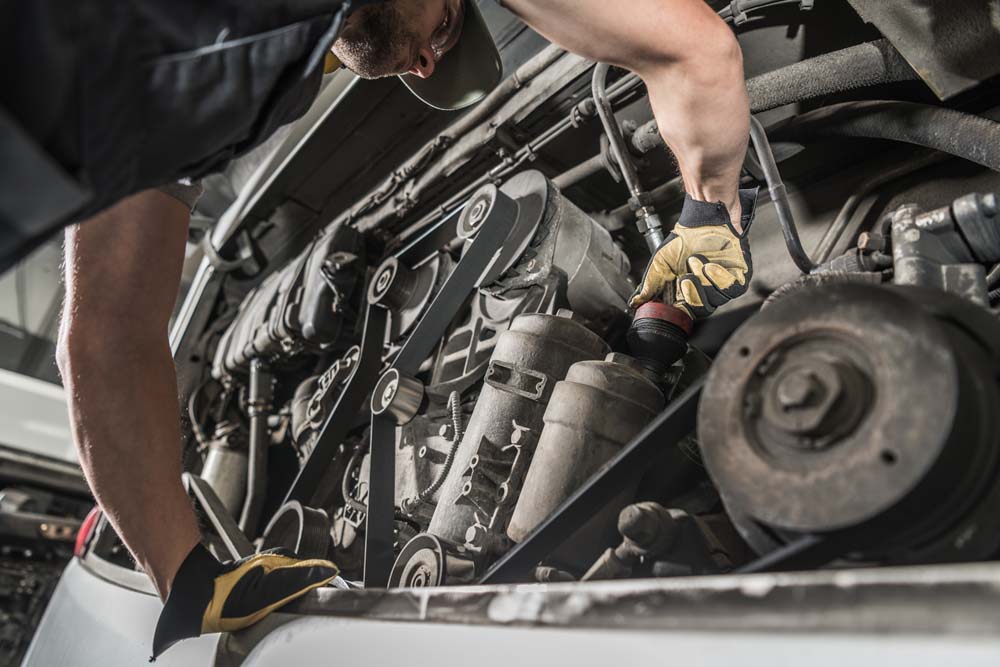
More News and Insight
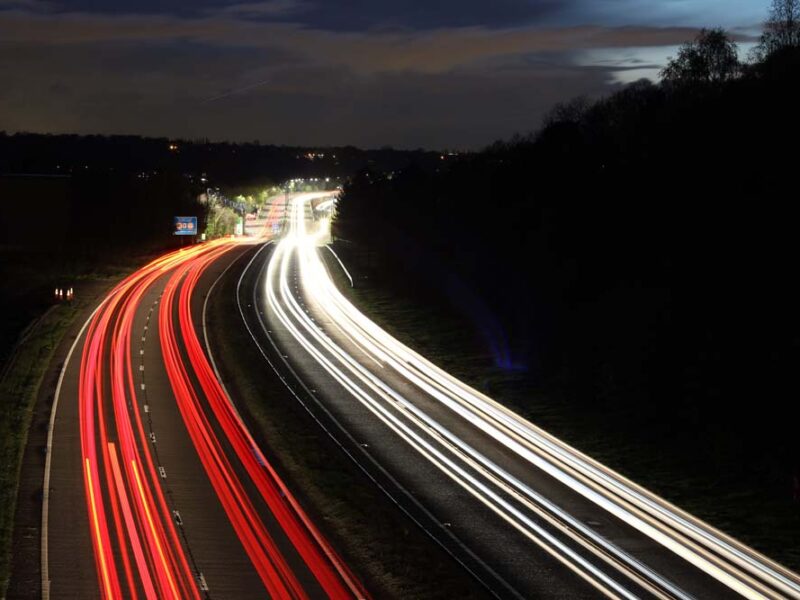
Changes to Brake Safety Inspections for Commercial Vehicles – April 2025
In April 2025 the brake testing regime guidance will change. Roller Brake Tests, that have been mandatory for years, will be joined by an Electronic Break Performance Monitoring System or EBPMS…
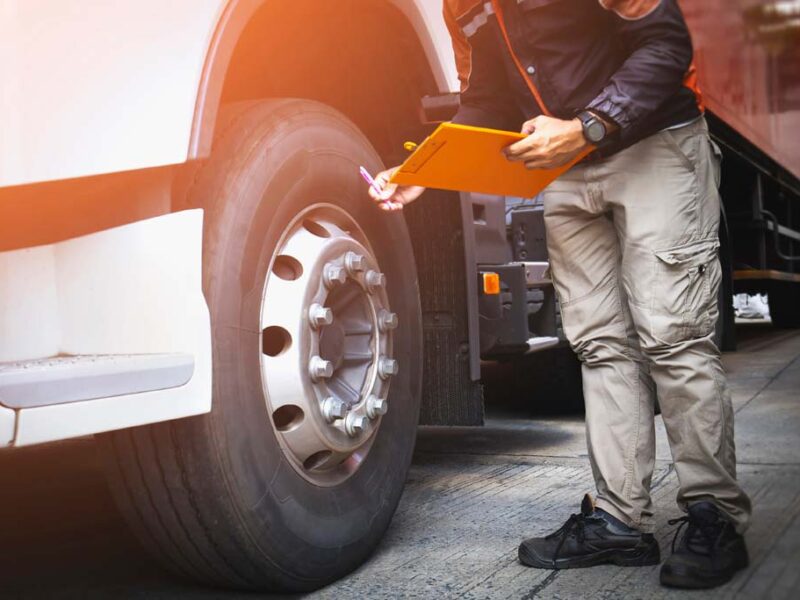
Case Study – Public Inquiry for Gillbard Plant, Autumn 2024
Gillbard Plant was called to Public Inquiry in Autumn 2024. The hearing made headlines in the transport press due to the element of “DVSA Poacher turned Game-keeper” of Gillbard Plant’s Transport Manager, Mr. Anthony Brayley-Willmetts, a former DVSA (VOSA) examiner turned transport consultant…
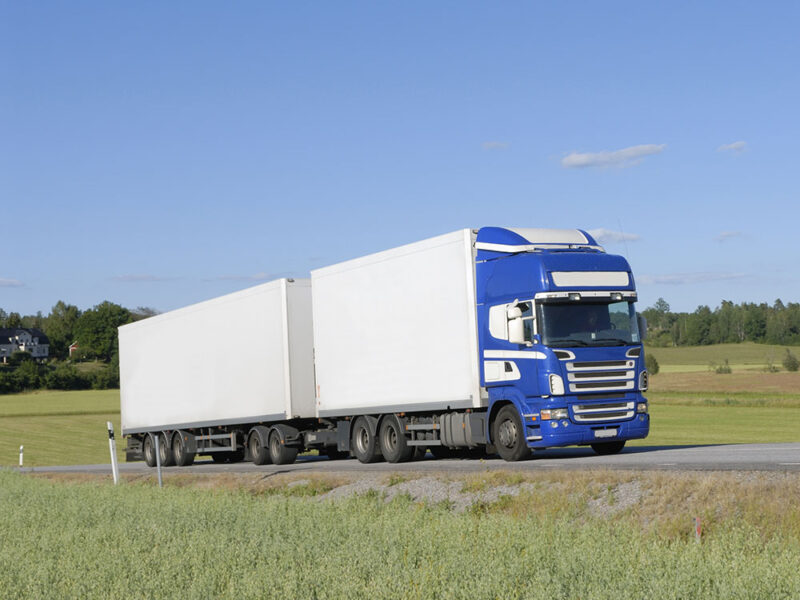
DVSA Load Security Guidance – Updated December 2024
When carrying loads on lorries every HGV Operator knows how important it is to ensure that goods are secured safely so that they arrive at their destination in good condition and that they do not cause any damage or danger on the UK’s roads during the process of transporting them…
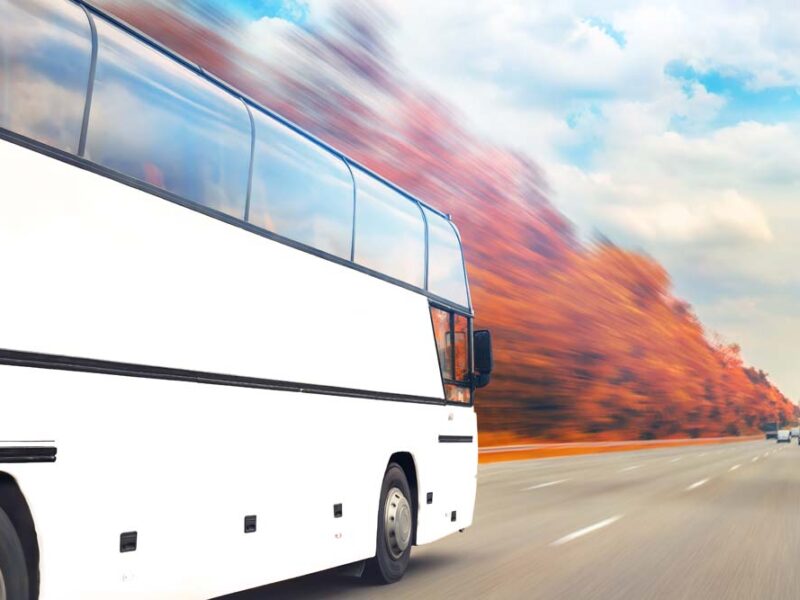
New Rules for Vehicle Operators and Drivers Carrying Out International Journeys
The Department for Transport and the Driver and Vehicle Standards Agency recently issued a bulletin regarding the new rules that vehicle operators and their drivers will have to comply with if travelling on international journeys…
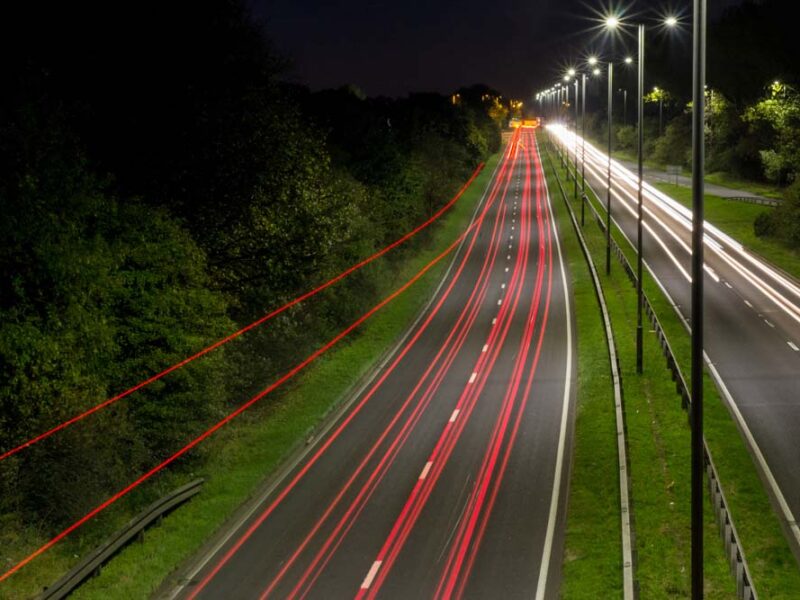
Road Haulage Association Members and DVSA Leadership Work Shadow Each Other!
To help highlight the Road Haulage Association’s “National Lorry Week” which this year was between 4th and 8th November 2024, the Road Haulage Association and the DVSA’s Leadership team decided to spend some time work shadowing each other….
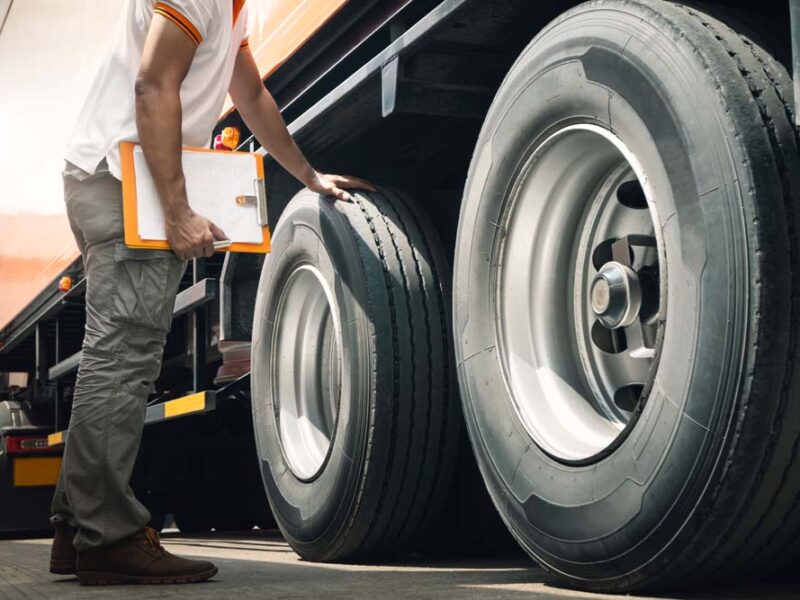
2024 Update to Guide to Maintaining Roadworthiness (GTMR)
The Guide to Maintaining Roadworthiness is the Driver & Vehicle Standard Agency’s (DVSA) standard produced in collaboration with key industry stake holders which explains the responsibilities and systems involved in maintaining vehicles in a roadworthy….
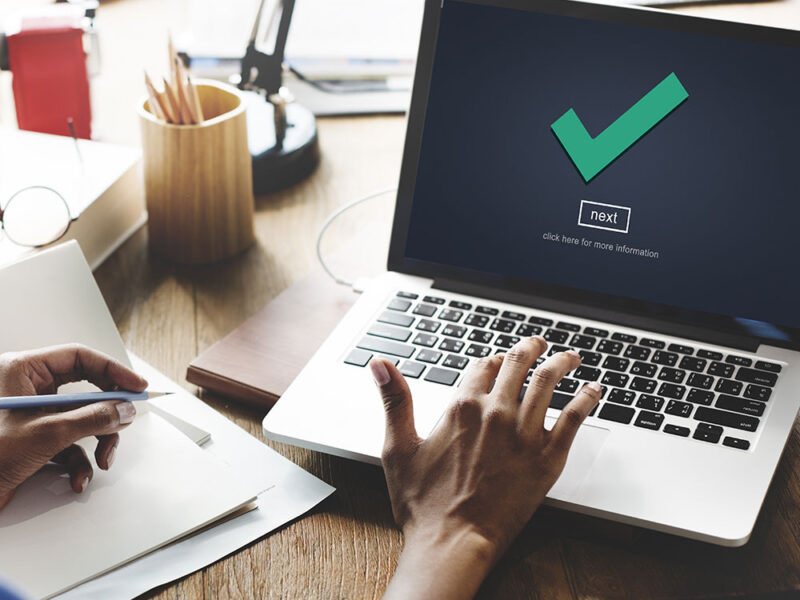
New Driver CPC Reforms to be in Force from 3rd December 2024
Following a very lengthy consultation period on this matter launched in early 2023, Parliament finally debated the “Vehicle Drivers (Certificates of Professional Competence) (Amendment) Regulations 2024” on Tuesday 29th October 2024…
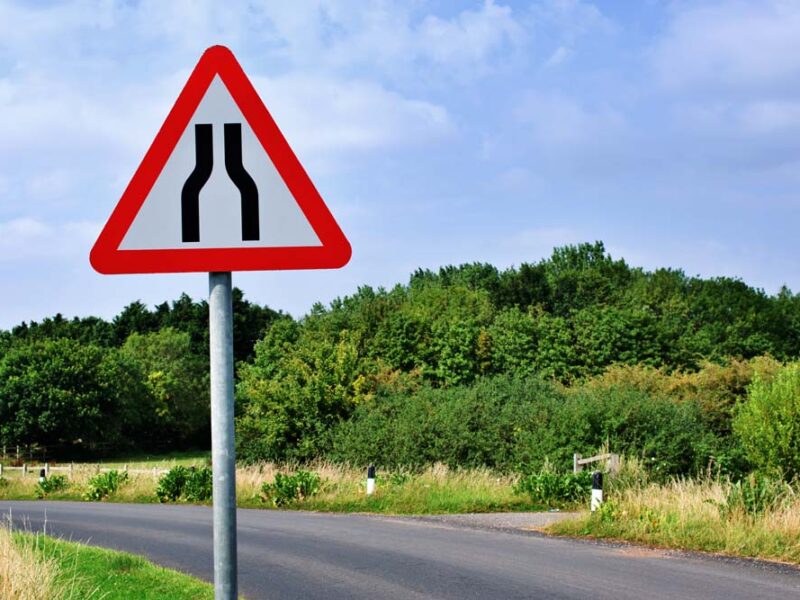
When Sat Nav’s Lead Lorries Astray!
Lorries getting into trouble and causing chaos in the small country roads of Great Britain have been making headlines again. Whilst a lot of this content is amusing and no doubt is a winner with internet audiences there is a very serious side to these incidents…

Traffic Commissioners 2023-2024 Report – the Highlights & the Lowlights of the Year
In early October the Traffic Commissioners of Great Britain published their annual report. The report encompasses the purpose of the individual Traffic Commissioners who are independent regulators for the goods vehicle and public service vehicle industries and their professional drivers…
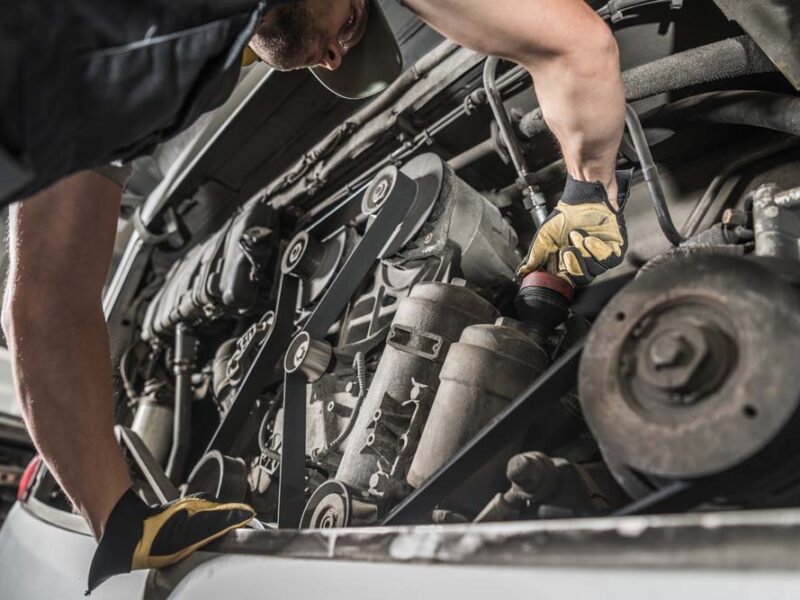
Vehicle Maintenance Data Collected by the DVSA
In a recent ‘blog’ by the DVSA’s Danny Charles the amount and type of data that the DVSA collects was discussed. Some may find it surprising how much data the DVSA holds and makes available to the general public on individual transport businesses…
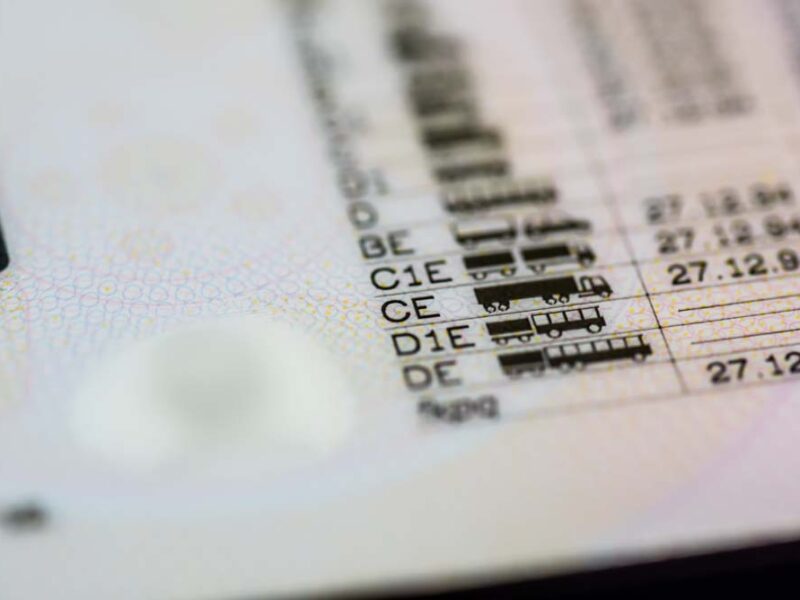
Murky Mini-Bus Waters in UK?
There has been reports in the industry news concerning the number of illegal operators of mini bus services who are operating un-hindered by the regulatory enforcement agencies…
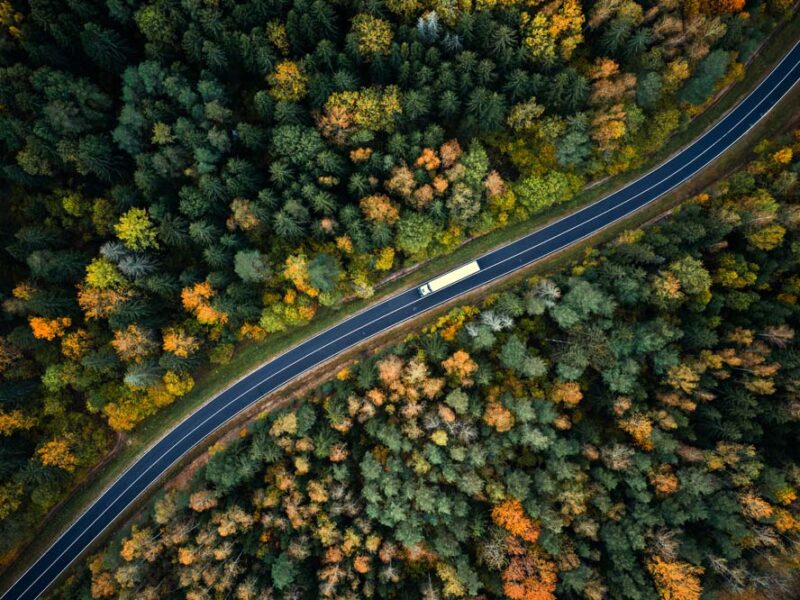
Driver CPC – Changes Coming in 2024 and 2025
The Driver Certificate of Professional Competence (DCPC) was introduced in the UK in 2007, as specified in EU Directive 2003/59/EC for all commercial drivers…