2024 Update to Guide to Maintaining Roadworthiness (GTMR)
The Guide to Maintaining Roadworthiness (GTMR) is the Driver and Vehicle Standard Agency’s (DVSA) standard produced in collaboration with key industry stake holders which explains the responsibilities and systems involved in maintaining vehicles in a roadworthy condition. The guide outlines the regulations, requirements and industry best practice that is recommended to properly maintain a fleet of commercial vehicles, including the daily checks, inspections and maintenance and record keeping that goes with running a fleet of commercial vehicles, large or small.
The guide, which can be viewed here has recently (5th November 2024) been updated in several areas, but the two key areas are;
- Brake Testing, and
- Safety Inspection and Repair Facilities
Brake Testing:
It had been rumoured that a change to brake testing “best practice” would be added to the guidance for a while now. The updated guide includes new sections on risk assessment and acceptable reasons for not being able to carry out a laden break assessment. The new section of the guide provides additional ‘best practice’ guidelines within section 5.3a “Braking Performance Assessment requirements from April 2025”. The guidance states that to follow best practice and comply with legislation there is an expectation that every safety inspection will include a measured brake performance assessment using either an Roller Brake Tester (RBT), a suitable electronic brake performance monitoring system (EBPMS) or a decelerometer with temperature readings.
On the subject of using a decelerometer, the guide states that it is “acceptable to use an approved and calibrated decelerometer to measure overall brake efficiency values for rigid vehicles without trailers or for vehicles that cannot be tested on a Roller Brake Tester (RBT) [but, whilst] a decelerometer will measure the overall brake efficiency, it may not identify individual braking issues”. The need to carry out a temperature check on all the brakes both before and after the decelerometer test to ensure that individual brake problems are identified, is highlighted in the guidance and it clearly states that where “satisfactory results cannot be achieved another method [to assess the brake performance of the vehicle] needs to be used”.
The updated guidance in section 5.4 on Electronic Braking Performance Monitoring Systems states, “if using EBPMS to monitor brake performance there must be an evaluation of the vehicle/trailer performance report before every safety inspection by a competent person who can interpret the data”. The guidance then goes on to state that the evaluation must be signed, dated and attached to the vehicle record together with the performance data report.
Safety Inspections and Repair Facilities:
Also in section 5 of the GTMR, the need to properly manage outsourcing of inspections and repair has been addressed. A new paragraph stating that “If you chose to outsource any of your maintenance you need to take steps to ensure the maintenance facility is adequately equipped and completes any work [done] to a satisfactory standard”. It goes on to say that “the quality of the work and the workshop facilities should be periodically reviewed by undertaking quality assurance checks”. A ‘fire and forget’ approach to 3rd party safety inspections will therefore need to be changed, with operators needing to record that they have the correct paperwork from vehicle maintenance providers and that they have actually reviewed and read the safety reports.
Sections with Additional Advice:
Wheels & Tyres:
There is additional advice in section 5.1 about refitting road wheels. The section states that the code of practice for the selection and care of tyres and wheels for commercial vehicles, which was developed by the Department for Transport and the British Standards Institute alongside industry and trade associations, recommends that following road wheel removal and refitting the wheel nut torque should be checked. Ideally this would be done after the vehicle has been stationary for 30 minutes or after it has travelled for between 40km and 80 km (25 – 50 miles in old money). The section states that all re-torque checks must be recorded and retained on the vehicle file. More information on wheel security can be found by clicking here.
Advanced Driver Assistance Systems (ADAS) – Section 5.6:
ADASs are a set of technologies that use sensors, cameras and software to improve a vehicle’s safety as well as comfort and convenience for the driver. An example might be early warning and detection of hazards in the road, blind spot assists and night vision systems. Many of these systems support safety critical systems such as braking or steering. It is unsurprising then that the guide requires that “effective maintenance procedures” are in place to “ensure correct functionality and that they deliver the road safety benefits they are capable of”. The section in the GTMR gives advice on recalibrating such systems if, for example, windscreens need to be replaced or if the engine control unit develops a fault.
PSV Automatic Vehicle Location Systems – Section 5.7:
These systems, often known as ‘AVLs” are computer-based technologies that track the location of a vehicle in real time and transmit that information to a central record or to the driver of the vehicle. AVL systems are most commonly used by PSV operators to improve service quality and efficiencies. The new version of the GTMR gives information on these technologies and reminds operators that they should ensure that the real time location data is being supplied before the vehicle is operated on a registered service.
Best Practice:
As always, the updated Guide to Maintaining Roadworthiness seeks to focus on what is Best Practice for transport operators. The Guide states that it is ‘not enough to rely on a maintenance system alone, because this cannot ensure that vehicles are roadworthy. To ensure best practice, you will need to combine good quality maintenance practices and skills with supervision and effective management of the system’. If that is something that you might need some help on, then the team at Pelly Transport & Regulatory Law has many years’ experience of setting up effective compliance systems for operators that are tailor made to each individual operation’s requirements. Call us now on 01279 818280 or click here to send an email. We are here to help.
© Richard Pelly, November 2024
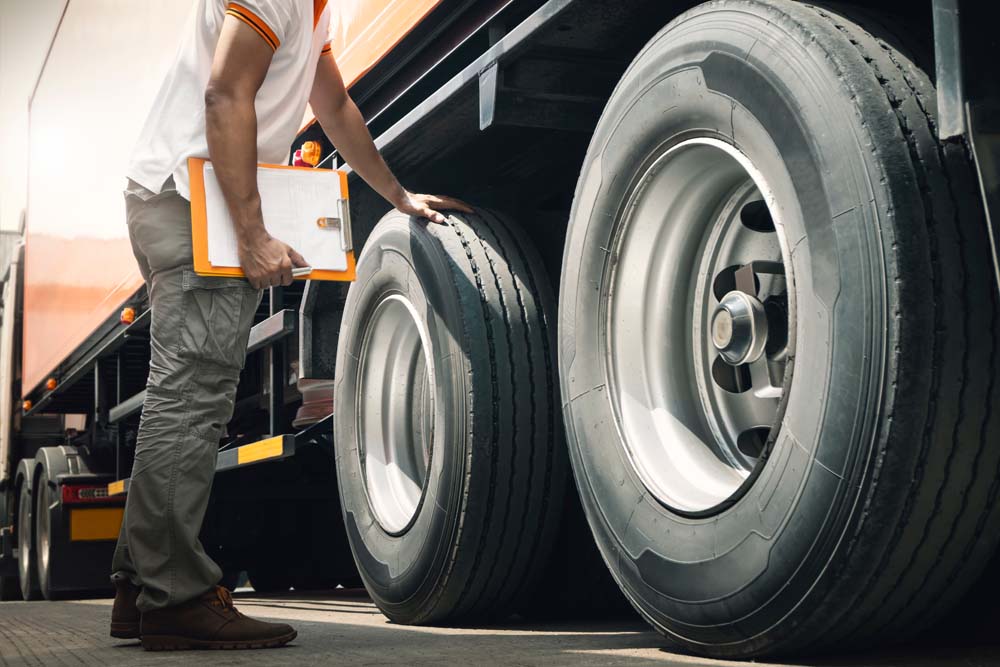
Latest Coach & Bus Industry News and Insight
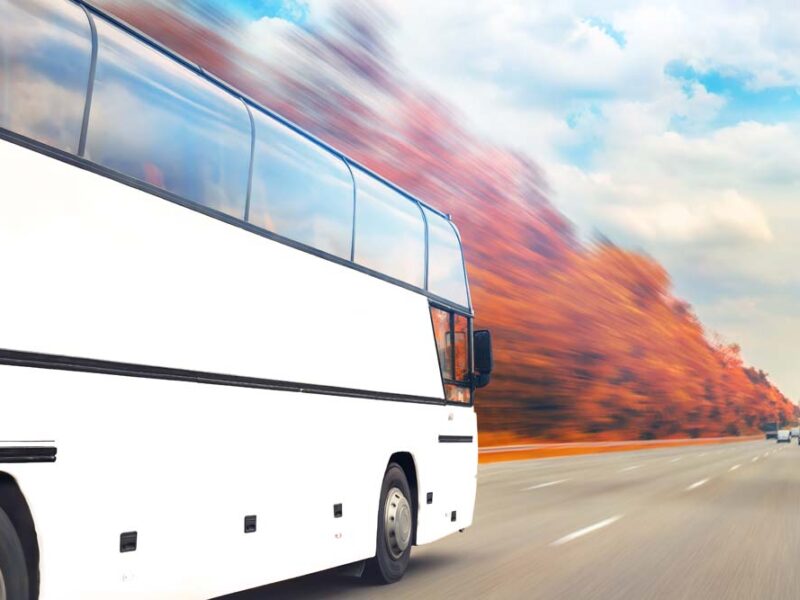
New Rules for Vehicle Operators and Drivers Carrying Out International Journeys
The Department for Transport and the Driver and Vehicle Standards Agency recently issued a bulletin regarding the new rules that vehicle operators and their drivers will have to comply with if travelling on international journeys…
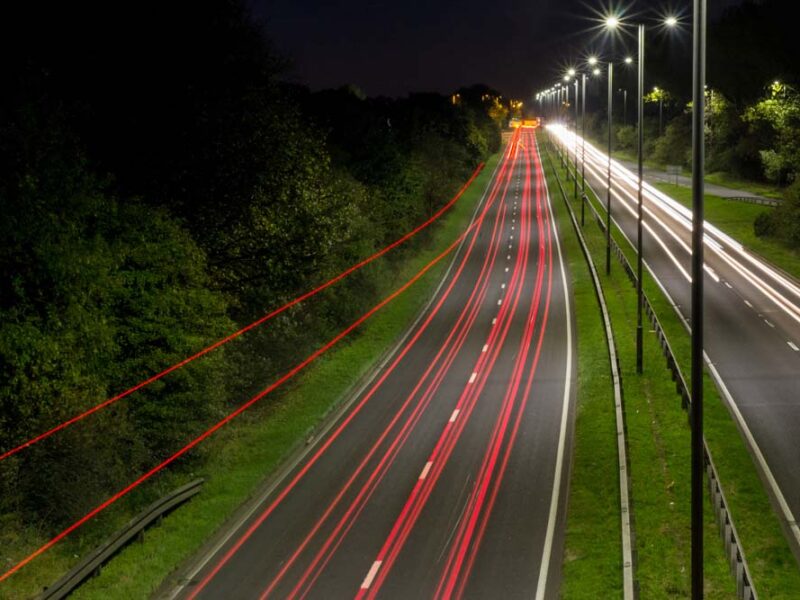
Road Haulage Association Members and DVSA Leadership Work Shadow Each Other!
To help highlight the Road Haulage Association’s “National Lorry Week” which this year was between 4th and 8th November 2024, the Road Haulage Association and the DVSA’s Leadership team decided to spend some time work shadowing each other….
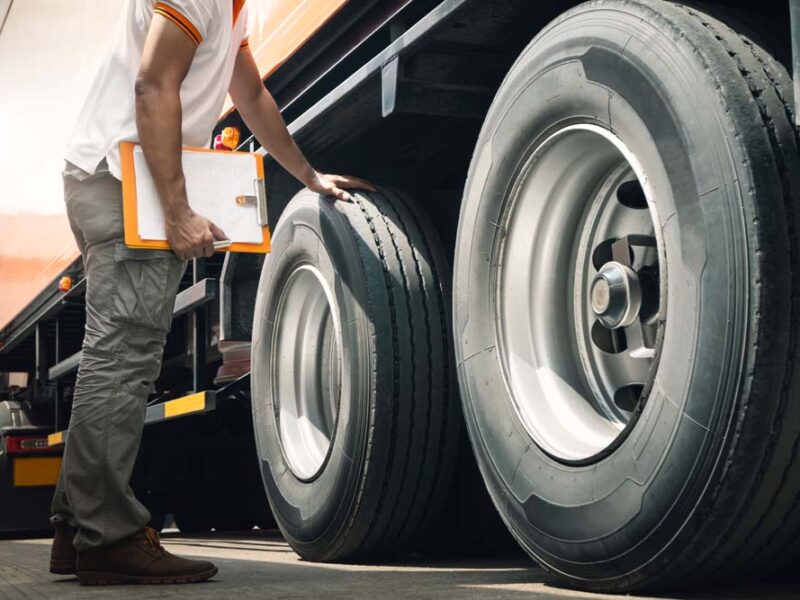
2024 Update to Guide to Maintaining Roadworthiness (GTMR)
The Guide to Maintaining Roadworthiness is the Driver & Vehicle Standard Agency’s (DVSA) standard produced in collaboration with key industry stake holders which explains the responsibilities and systems involved in maintaining vehicles in a roadworthy….
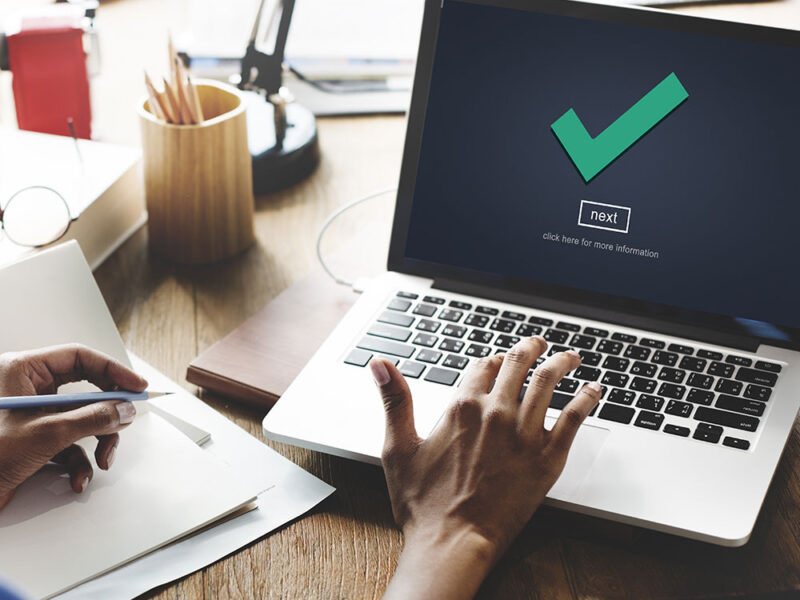
New Driver CPC Reforms to be in Force from 3rd December 2024
Following a very lengthy consultation period on this matter launched in early 2023, Parliament finally debated the “Vehicle Drivers (Certificates of Professional Competence) (Amendment) Regulations 2024” on Tuesday 29th October 2024…
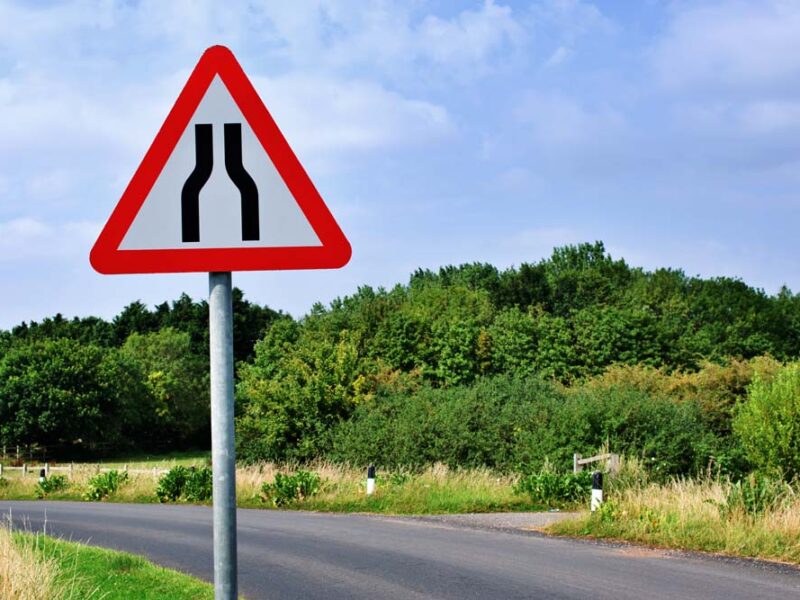
When Sat Nav’s Lead Lorries Astray!
Lorries getting into trouble and causing chaos in the small country roads of Great Britain have been making headlines again. Whilst a lot of this content is amusing and no doubt is a winner with internet audiences there is a very serious side to these incidents…

Traffic Commissioners 2023-2024 Report – the Highlights & the Lowlights of the Year
In early October the Traffic Commissioners of Great Britain published their annual report. The report encompasses the purpose of the individual Traffic Commissioners who are independent regulators for the goods vehicle and public service vehicle industries and their professional drivers…
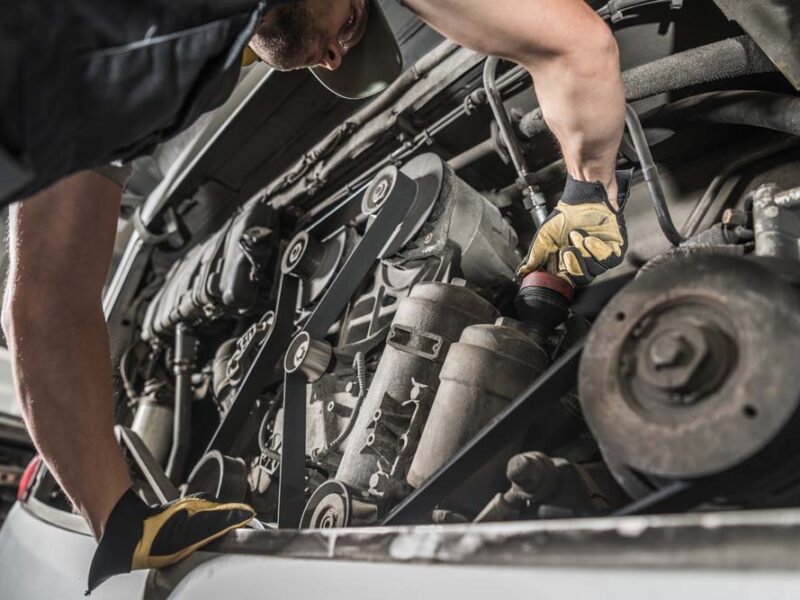
Vehicle Maintenance Data Collected by the DVSA
In a recent ‘blog’ by the DVSA’s Danny Charles the amount and type of data that the DVSA collects was discussed. Some may find it surprising how much data the DVSA holds and makes available to the general public on individual transport businesses…
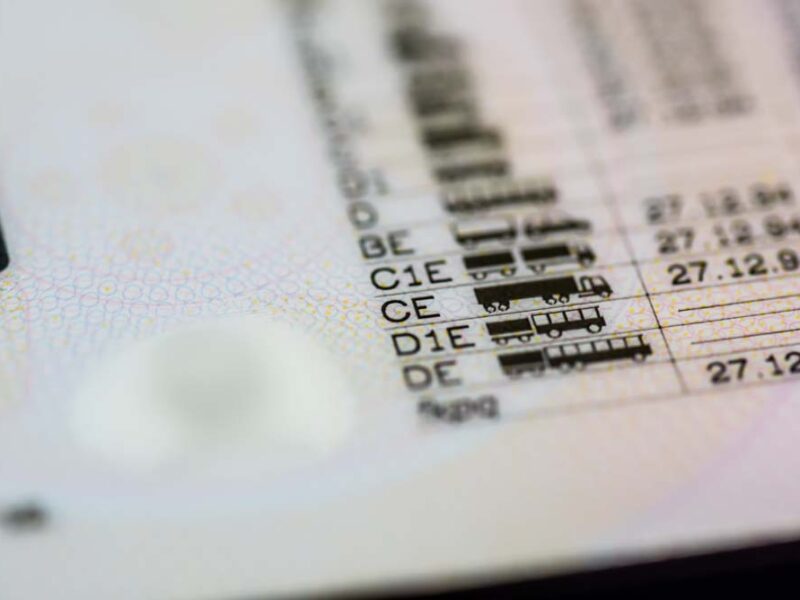
Murky Mini-Bus Waters in UK?
There has been reports in the industry news concerning the number of illegal operators of mini bus services who are operating un-hindered by the regulatory enforcement agencies…
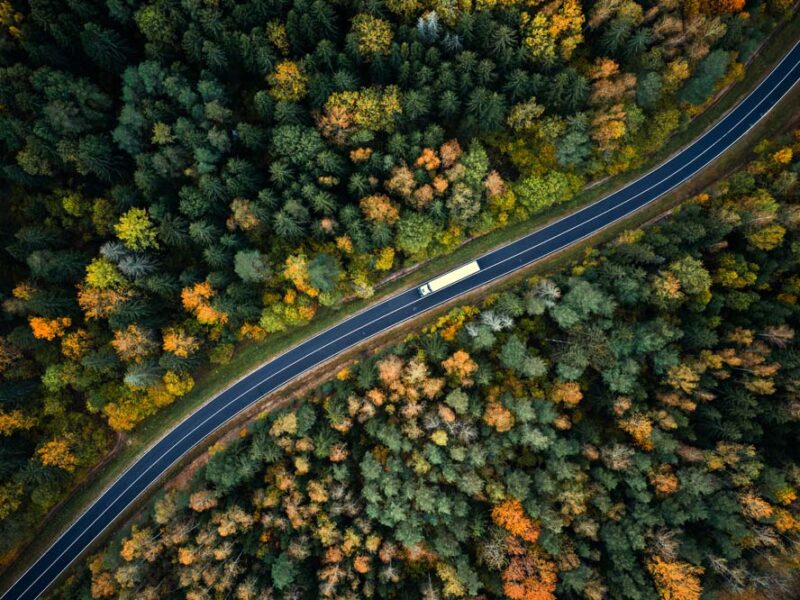
Driver CPC – Changes Coming in 2024 and 2025
The Driver Certificate of Professional Competence (DCPC) was introduced in the UK in 2007, as specified in EU Directive 2003/59/EC for all commercial drivers…
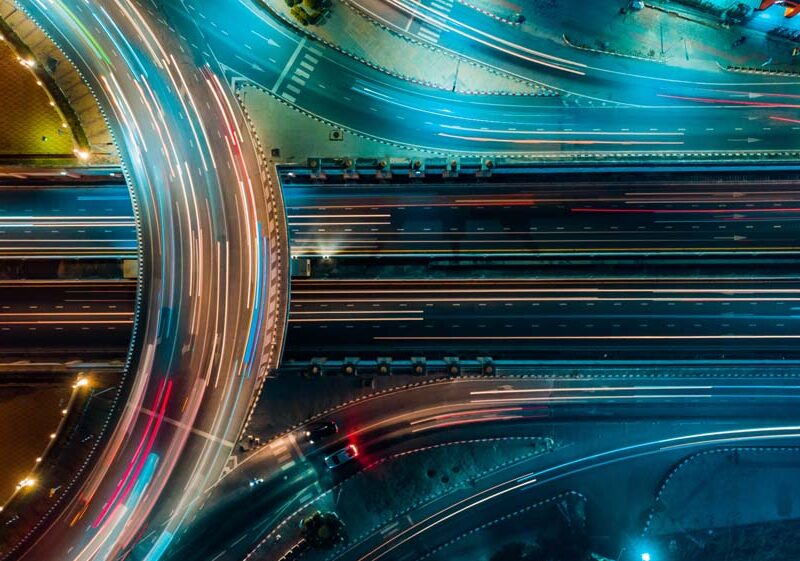
Driving in the UK? Read about the latest Rule Changes in 2024
Earlier this year various new driving laws were introduced, impacting both standard road users as well as HGV and PSV road users across England, Wales & Scotland. If you are driving in the UK, especially if you are a commercial driver, then you should ensure that you are aware of these amendments and new rules…
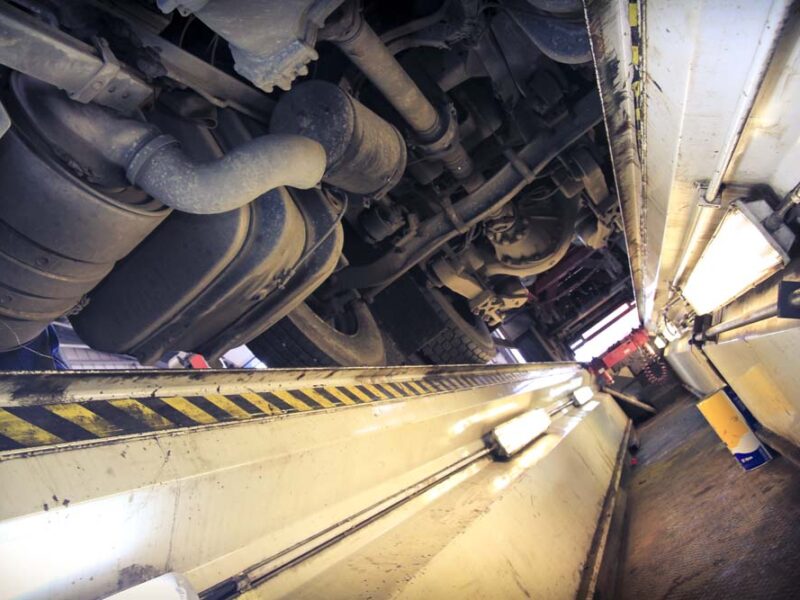
Are You Taking your Responsibilities to Maintain your Vehicles Seriously?
Running a haulage business is not an easy undertaking. There are a multitude of decisions to be made on a daily basis before any driver actually gets behind the wheel and delivers the goods (or passengers!).
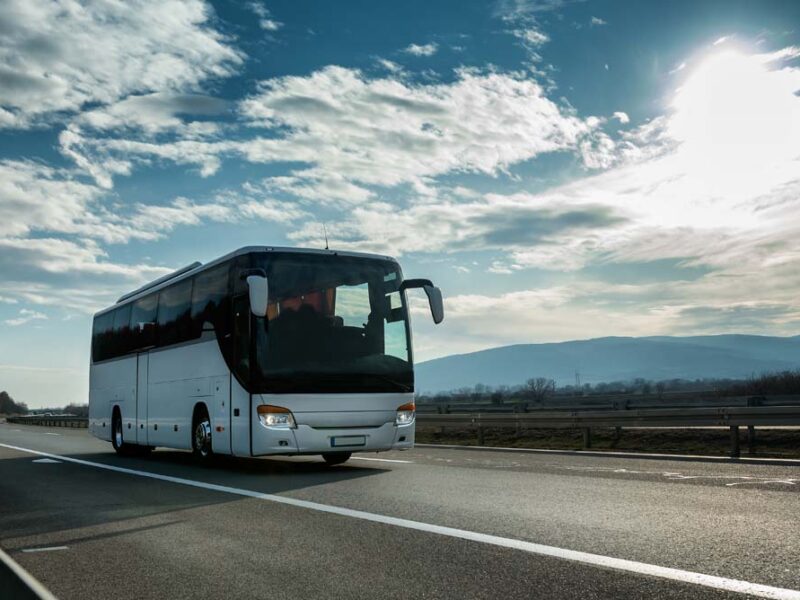
Update to the Guide to Registering & Operating Local Bus Services in England & Wales
The Senior Traffic Commissioner’s guide to registering and operating local bus services in England and Wales is intended to help operators of local bus services understand the requirements for registering a service.